A Brief History in Advancing the Performance of Polyester
Polyester has had a place in our lives since the 1940s, when John Rex Whinfield and James Dickson were attributed with the invention of the original polyester fiber. It was first commercialized by ICI under the brand Terylene, and further enhanced with the brand Dacron, which was launched by E.I. Dupont in the early 1950s.
Despite a rough few years in the ‘70s (the age of the Leisure Suit), today’s polyester has become an industry-leading textile fabric for performance wear, outerwear, fashion basics, caps and bags. Over the years advances in technology have yielded many reasons to use polyester over other fabrics, including:
- Fibers are durable and lightweight, which is great for athletic wear
- Naturally wrinkle resistant and easy to care for
- Dries quickly, making it ideal for outerwear
- Retains its shape better than its cotton alternative
- Highly stain resistant, making it easy to clean
- More economically priced compared to other synthetic options, such as Nylon
Unfortunately for the garment decorators of the world, there is a natural enemy waging conflict with polyester fibers daily: Heat!
As the saying goes in screen print shops, “heat builds.” From exposure to flash units, heat accumulation of platens, curing dryers, hot stacking, and overall shop environment temperatures, heat is unavoidable when it comes to screen printing apparel.
Once upon a time this created a very challenging scenario where the screen printer was constantly battling polyester dyes and their negative relationship with plastisol inks.
Because polyester is a synthetic fiber, standard textile dyes have a limited ability to saturate and absorb into the filament. While cotton is porous and absorbent, polyester tends to hold onto that dye saturation very loosely. That means when the polyester fiber is exposed to heat (typically approaching 300 degrees), that loosely held dye can return to a gaseous state and release from the filament and flow freely throughout the garment.
What does this mean for the screen printed or heat applied design on that polyester piece? Trouble!
That gaseous free-flowing dye can then infiltrate the plastisol ink through a process known as dye migration. This process can have devastating effects to the intended colorway of the print, as it transitions the intended color of the print into a muddled combination of the shirt dye.
Red shirts and white ink? Hello pink!
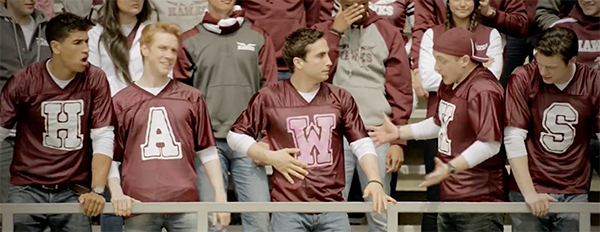
This transformative process can happen immediately, or it may take hours, days, or even weeks. Freshly-printed shirts may look impeccable right off the dryer, only to have the end user’s unboxing experience turn sideways when they see a miscolored print staring back at them.
One of the earliest processes created for combating this undesirable occurrence was the formulation of low-bleed athletic inks that were built specifically for synthetic fiber application. These inks tend to be extremely viscous and are optimized to combat dye migration by flashing and curing at lower temperatures than standard plastisol inks.
However, due to their thicker viscosity, these inks also need to be sent through coarse mesh sizes to fully transfer through to the shirt, which means that logos and emblems often must be simplified and lacking in tight detail for the design to be fully realized.
In 2012, with the world of screen print inks going through consistent formulation changes to attempt to combat dye migration successfully, SanMar set out to solve the problem at its root cause: the dye itself.
Enter cationic dye, or as we have trademarked it here at SanMar, PosiCharge!
What Does PosiCharge Mean?
Our Glossary of Terms on sanmar.com identifies what the science behind our PosiCharge technology is all about:
PosiCharge Mesh®
Water-soluble dye process that breaks apart, or ionizes, in the dyeing solution to give off a positively charged colored ion. The cationic ions dye the polyester fibers by linking with the acid groups on the fibers – locking in the color. This results in a better, bleed-resistant, colorfastness.
In other words, this cationic dyeing process directly affects the polyester filament, preventing the dye from releasing at extreme temperatures and allowing the integrity of the intended ink color to remain.
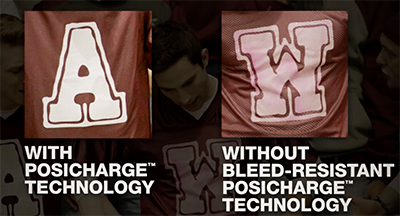
The game-changing end result is a polyester fabric that won’t bleed and prints easily, keeping logos crisp and clear.
What Printing Advantage Does This Give Me?
Increased confidence that your hard work and intended results are less likely to be affected by unwanted external factors.
Try as one might, maintaining a consistent shop temperature can be extremely challenging as a garment makes its way through the steps of receiving, check-in, pre-production, production, post-production, and shipping/pick-up.
With PosiCharge styles, printing concerns can be minimized with the knowledge that your canvas has a bleed-resistant technology built right into the fabric.
However, that isn’t to say that all precautions should be thrown out the window – after all, we’re still dealing with polyester which, inherently, has a lower heat tolerance than many other textile fabrics for multiple reasons.
So What Type of Ink Should I Use?
It’s highly recommended that low bleed and low cure inks that cure at or around 270 degrees are still implemented when decorating PosiCharge styles. One Stroke Inks have developed a line of Low Cure Inks that feature multiple benefits across their various lines, including smooth viscosity, soft/stretchy/matte finishes, and maximum opacity formulations.
The benefits of PosiCharge don’t live in a vacuum, and those benefits should be viewed more as an added layer of protection against dye migration that work in concert with other mitigating resources. Plastisol inks have come a long way and some of these recipes are now more capable of being passed through a finer mesh screen than they were a decade ago.
So while we still recommend you utilize low cure/low bleed inks, try testing what using LESS of those consumables looks like on your PosiCharge garment. Instead of decorating a lightweight performance fabric with a heavyweight print, incorporate a smoother viscosity low bleed ink and lay down a lighter layer of ink deposit through a finer mesh to capture more detail.
Should I Still Use an Underbase?
Don’t think that PosiCharge is synonymous with an optional underbase when printing on dark garments, which is a common misconception.
Light still plays a factor in how printed colors are perceived on darker shirt dyes, regardless of the fabric or technology behind them. Simply put, a single layer of ink deposit, even of the thicker low bleed variety, can still allow light to penetrate through and bounce off the color of the garment, creating a distortion in how the ink color is perceived.
Flashing a grey underbase and laying your highlight colors on top of it will not only eliminate light penetration, but it’ll also serve as that ultimate protective barrier to prevent dye migration in tandem with the beneficial bleed-resistant technology inherent in PosiCharge styles.
What Are Some Best Practices to Consider?
In addition to the tips listed above:
- Consider using a donut probe to test the temperature of your dryer prior to production. An infrared temperature gun, while certainly viable, will only identify the temperature of the print’s top layer. You want to make sure that the ink is cured all the way down to the bottom layer touching the garment, and a donut probe will help you identify the temperature of the dryer from start to finish. Since the goal for printing on polyester is to maintain low heat, this accuracy measuring tool can quickly become your best friend.
- Avoid hot stacking! We often think about temperature in relation to our equipment but fail to remember that (as mentioned earlier) “heat builds!” That includes your shirts exiting the dryer and falling on top of themselves in a catch bin, which can cause unwanted ramifications such as ghosting and zebra striping. To prevent this, make sure you have a dedicated individual ready to collect each shirt as it exits the dryer to promptly place them in a cool down station prior to packaging.
- Also consider implementing a fan at the end of your dryer to work on bringing the garment temperature down as quickly as possible upon departure from the chamber.
A Decade of Decoration
Polyester has certainly come a long way from the Leisure Suit debacle of the 1970s. In fact, it’s fascinating to think about how much polyester has been incorporated into our lives across so many different lifestyle categories outside of wearables; tents, carpet, upholstery, safety belts, laundry bags and many other applications use polyester today.
It’s also worth looking back on a time, not that long ago, when printing on polyester was more akin to the Wild Wild West, with very little guidance, resources or consistency to speak of.
PosiCharge now has more than 10 years to its name, which means a decade of reduced frustration when decorating on polyester fibers. It has been a decade to celebrate, as this cationic dye recipe has assisted in making print shops of all shapes and sizes much happier when an order of polyester goods comes through the door.
If you ever have any questions on how our garments can be decorated (regardless of technique), don’t forget to consult our Decoration Spec Sheets, which identify where, how, and how big every garment in our assortment can be decorated. You can also reach out to decoratorrelations@sanmar.com for additional guidance and information.