Waterproof and water-resistant apparel is one of those decorating challenges that seems straightforward but can quickly become complicated. There are a lot of variables to consider between the fabric you’re working with, the decoration method and your customer’s needs.
That’s why we’ve put together this quick guide. Keep reading for some general advice, or scroll down to see specific recommendations for embroidery, heat transfer and screen printing.
Ask Questions & Test, Test, Test
Before you start, talk to your consumable supplier. They’ll know which products are built for waterproof fabrics and how to apply them.
Next, plan to test one or two pieces before going into production. Few things are worse than running a 50-piece order and having the job sent back because the decoration failed.
Yes, this is basic advice. But you’ll thank yourself for taking these simple steps, especially if you’re decorating a particular fabric for the first time.
With that in mind, here’s some more specific guidance for the three most popular decoration methods for embellishing waterproof fabrics.
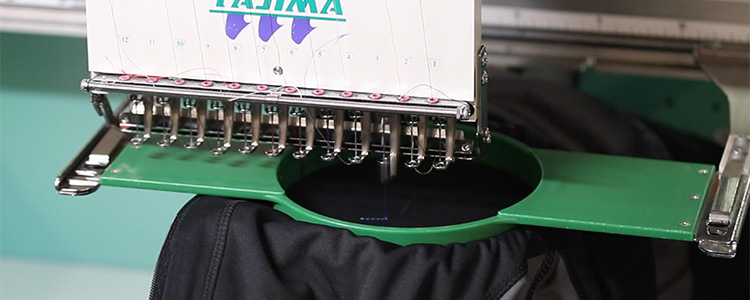
Embroidery
Embroidery tends to be the most straightforward way to decorate waterproof fabrics. Sewing on a waterproof jacket or fleece is like sewing on any non-waterproof fabric.
The difference is when you need to waterproof the area being embroidered itself.
Embroidery creates thousands of tiny holes in a concentrated area, which compromises waterproofing. This isn’t a big deal for some customers since the affected area tends to be small: left chest, nape of the neck, etc.
But others will want to maintain the waterproofing element throughout. In those cases, it’s best to incorporate a laminate backing. This will seal the embroidered area during decoration and help maintain the integrity of the waterproofing element.
E-Z Film Laminate from Madeira is ideal for sealing up the back side of embroidery on waterproof garments. Here’s how to use it:
- Cut a piece of laminate that’s slightly larger than the embroidered logo
- Turn the garment inside out
- Lift the decoration area up from the platen with the help of a Heat Press Pad
- Cover the laminate with a protective barrier
- Press the laminate onto the substrate at around 255°F for 15 seconds
- Let the laminate cool
- Peel the release paper
Your laminate is now adhered to the substrate and will successfully waterproof your embroidery.
You can also use film laminates to finish off the back sides of patches and emblems.
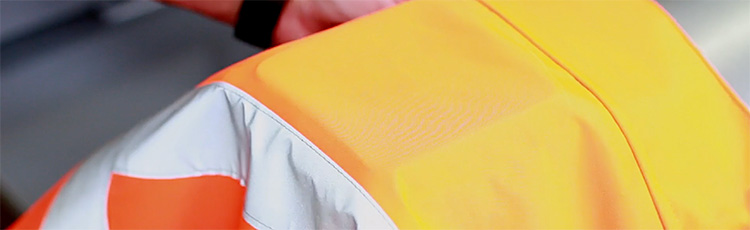
Heat Transfer
Heat transfer technology is on the rise, and Direct to Film is taking the industry by storm. So it’s likely a customer will ask about this (if they haven’t already).
The key to a successful heat transfer on waterproof fabric is to ensure that your transfer has a strong hot melt powder or aggressive adhesive.
For single-color decorations on nylon, oxfords, satin and waterproof bags, Gorilla Grip II is still a great solution thanks to its intense grip and high opacity.
Multicolor, direct-to-film decorations can be tricky. If you try to decorate waterproof fabric with standard powder adhesives, you may find that the transfer peels right off. That’s because the thermoplastic polyurethane powder made for in-house printers is a poly-based adhesive. It doesn’t have the aggressive properties required for more challenging substrates.
If you’re making your own prints in-house, contact your consumable supplier to see what options they have available.
If you have a more challenging job on your hands, consider outsourcing to a trusted industry supplier. Here are a few we recommend:
- Supacolor’s Promotional Transfers are a hybrid direct-to-film/water-based ink that incorporate a super strong adhesive. It has consistently performed well on waterproof outerwear, and nylon products like bags and umbrellas.
There’s no bleed resistance to this product, but it can be applied as low as 260°F, which can help minimize discoloration. However, if you have a large white design on red or maroon fabric, this may not be an ideal fit.
- Supacolor’s Softshell Blocker is, as the name suggests, made to adhere to softshells and outerwear with waterproof coatings. It includes a softshell dye-blocker layer between the adhesive powder and ink, which prevents dye migration and cures at a standard 290°F.
- We’ve also seen successful application of heat-applied patches and emblems on waterproof outerwear. Products like STAHLS’ PVC Patches are a unique way to impress your customer with a dimensional logo that lends itself to application on heavyweight fabrics like jackets and backpacks. Securing the patch by circling the logo with a sewing machine can help ensure adhesion and efficacy.
Like we mentioned above, consulting with your consumable supplier about these products—and testing them—is of the utmost importance.
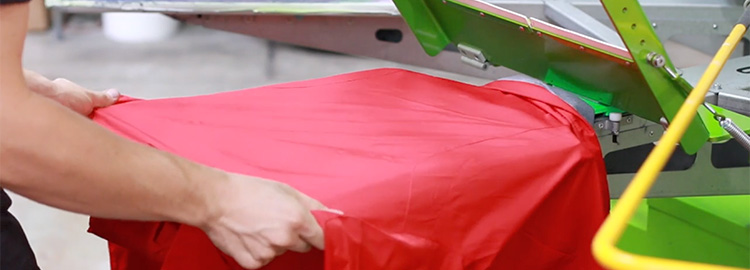
Screen Printing
Screen printing on waterproof fabrics comes with its own set of unique circumstances. Here are some tips to help you tackle the job:
- For outerwear, evaluate the need for a functioning clamp to accommodate any double-ply styles. Two-Ply Hold Downs from Action Engineering are ideal.
- Don’t forget about zippers. Consider investing in Zipper Hoodie Pallets, which creates a central channel for that zipper to lay in and provides a level decoration surface for the squeegee to pass over.
- Have a plan for adhesion. You can incorporate a bonding agent, like the Catalyst 900 from International Coatings, into any plastisol ink to improve adhesion on challenging fabrics. You’ll still need to cure the ink at its standard temperature. The catalyst will help harden the ink over 24-48 hours.
When using a catalyst agent, try for a 10% ratio of catalyst to ink, and only add the agent to the ink pot while it’s on the screen. The catalyst will compromise and harden any ink it encounters, which would be bad news for the 5-gallon container of ink you use on a regular basis. Discard the ink immediately after use to ensure you preserve the screen for the next job.
If you’d rather not use a bonding agent, you might try the International Coatings All Pro 900 Series. It’s a fast-flashing, two-part ink formulated for printing on hard-to-print fabrics like nylon. The harder finish resists scratching, scuffing and peeling for an extremely durable image.
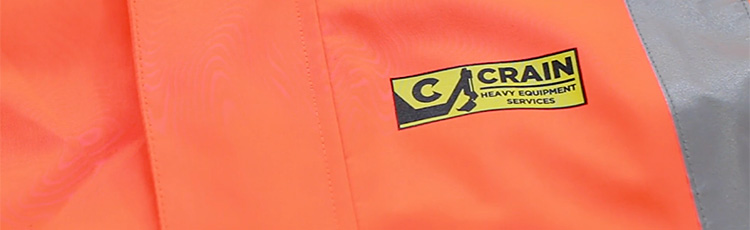
Best Practices for Decorating Waterproof Fabrics
In closing, a few parting bits of advice:
- Testing is of the utmost importance. When in doubt, order an extra garment and include the cost in your pricing.
- Let the artwork lead the way. If it’s not an ideal fit for your customer’s preferred decoration method, don’t be afraid to tell them so. You’re the expert, so share your honest thoughts on why they should consider a different process in this case.
- Color count matters. Screen printing may not be the best option if there’s more than one color in a design. Many waterproof fabrics are sensitive to heat and could be difficult to flash between colors when screen printing. If this is the case, consider embroidery or heat transfers.
- Durability is a factor. Outerwear typically isn’t laundered frequently. Performing a scratch test after a heat transfer or screen print is applied is usually enough to see if it will last. When in doubt, conduct multiple wash tests to evaluate results.
Decorating waterproof fabrics can be challenging. But it’s also extremely rewarding to pull off a complex job for another happy customer. We hope this guide helps you tackle your next big project.